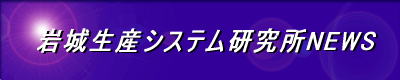 |
発行者 岩城生産システム研究所
編集者 IPSインターナショナル |
平成23年01月15日発行 第130号 |
|
― 目 次 ― |
◆ 「わたしの理解したトヨタ生産方式 その4」 ルネサスセミコンダクタ九州・山口梶@熊本錦工場 佐藤 光信 様
◆ 「確実に広がるトヨタ生産方式」 岩城生産システム研究所 岩城 宏一
|
|
「私の理解したトヨタ生産方式 その4」 |
 |
ルネサスセミコンダクタ九州・山口株式会社 熊本錦工場 佐藤 光信 様 |
1.はじめに
4回目の投稿である。前回(第94号)はNECグループの半導体製造会社の立場で、そして自動車の販売台数が過去に無い落ち込みから脱し、ハイブリッド車を中心に急激に需要が回復を始め、これに追従した半導体所要の急増に一丸となって対応している時期であった。あれから1年、新ルネサスグループへの移行という事業環境の変化と同時に、旺盛な所要に支えられ最大の生産を続けてきた。 しかし今下期に入って一転、エコカー補助金制度の終わりを契機とした需要の落ち込みに引っ張られ、我々も弱含みの生産を強いられている。
岩城先生の指導を受けて始めた物流しの改革も、このような環境激変の中、トヨタ生産方式の常識を覆す新たな領域に歩を踏み出し始めている。これは先生の指導を受けない弱みを逆手にした新たな挑戦と考えており、“トヨタ生産方式の進化系Nishiki”と称し活動を進めている。正しく今までの活動の中から得た「私の理解したトヨタ生産方式」そのものである。
2.そもそもトヨタ生産方式の原則って何?
かんばんを用いて前店で買い物をするには、そこに買うべき品物と量がなければならず、すなわち《店には決めた品が決めた量ある》のがトヨタ生産方式の原則(常識)であることは言うまでもない。
この原則遵守に向けた努力をしながら、後工程かんばん引取り方式の完成をめざして活動を進めて来た結果、工程内の物流しが平準化に近づき、仕掛数量が激減したことにより、リードタイム短縮でも大きな成果を得ることができた。しかし、ここ暫くはリードタイムの下げ止まり状態が続いていた。この打破を最大のテーマとして2010年度から新たな思考による物流し改革に取り組み始めた。
3.トヨタ生産方式とリードタイムの関係を考える
改めて後工程かんばん引き取り方式の特徴を紐解くと、Σ(生産指示かんばん枚数)でリードタイムが決まる、言い換えれば生産指示かんばん枚数を減らせば比例してリードタイムが短くなるという極めて手段が明らかで有効な物流しと言える。
しかし我々が流す製品には、世に言う“繰り返し生産品”はほとんど存在せず、日当り出荷かんばん枚数が2枚なんていうのもごく普通であり、結果として各店の欠品も品種によっては常態化してしまう。
このことがリードタイムの下げ止まり要因の一つになっていた。なぜなら、日当り出荷かんばん枚数が極少だからと言って、出荷かんばん枚数の多い製品と同じ比率で工程内の生産指示かんばん枚数を減らすことは、トヨタ生産方式の原則(店には決めた品が決めた量ある)からして絶対にできないからである。したがって、リードタイム短縮に最も効果を発揮するはずのトヨタ生産方式も、繰り返し生産品の少ない生産環境下且つ、後工程引き取り生産方式があるレベルに達した以降はリードタイム短縮の弱点になってしまう、と勝手に結論づけた。
4.店は欠品でもいいんじゃないの?との逆発想で
3項で述べた通り、トヨタ生産方式の原則の中でリードタイムを短縮するには限界があると理解し、逆発想に転じた。すなわち《店に物が無い状態》を常態化することにしたのである。有る物を買って帰るトヨタ生産方式の絶対的思考から、後工程が買い物する品を先に予約し、それに前工程が対応する思考へと、考え方を全く逆にしたのである。 ※店に物が無い状態とは:店の間口のみ残して奥行きを無くした状態を言う。
4−1.リードタイムを短縮するにはロットの停留時間を最短にすべき
《店に物が無い状態》の常態化がリードタイム短縮への必須条件との信念に基づき、次に述べる2つを具体策として考案、そして実践することで、ほぼ期待する成果を手中にしつつある。いずれも、物を持たない店に買い物に行くことにより、加工済みロットが停留することなく後工程に引き取られることを目的としている。
具体策1:生産能力に余裕がある生産ラインへの適用策
工程内の生産指示かんばん枚数(=標準手持ち量)を徹底して減らすことと並行し、店の標準手持ち量を“0”にすることにより、トヨタ生産方式の4つの仕掛けの一つである「後工程から引かれた分だけ造る」という約束も、理屈を理解した上で棚上げした。生産指示かんばん枚数を減らし、それ見合いにかんばん運用の回転を上げることで、加工済ロットが工程内や店に停留することを排除したのである。
本思考の代表例を紹介する。ソフトクリーム販売方式と名づけた引取り方式である。旧方式をあえてアイスクリーム販売方式と呼ぶことにより、目的の違いを明確にしている。さながら冷蔵庫に保管して販売、売れた分だけを補充するアイスクリーム販売方式から、お客様の注文を受けてから作って手渡すソフトクリーム販売方式、すなわちみずすましは次期タクトで買い物する品を現タクトで予約、前タクトで予約し前工程が補充してくれた品を現タクトで引き取る方式に変更することで、店の手持ち量“0”と工程内の標準手持ち量“減”を実現した。この両者の違いを次図に示す。
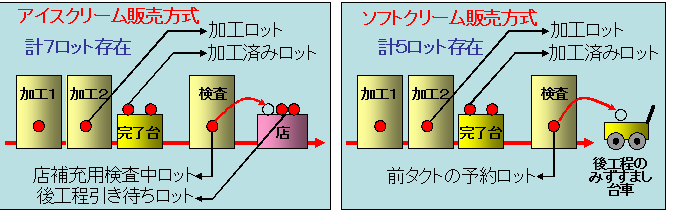
具体策2:生産能力がタイトで余裕の無い生産ラインへの適用策
具体策1と方法が全く異なる、生産指示かんばん枚数を増やすことにより工程内や店にロットが停留することを排除する“幸せの黄色いかんばん方式”なる方法を導入した。次図に概要を記すが、これはネック工程の頑張りで一日の引き取り枚数が決ってしまうような、比較的工程能力に余裕の無いラインに適用しており、ネック工程のトラブルで前工程への引きが弱まることの防止を目的に、ネック工程の少しの工程余裕分に黄色い生産指示かんばんを追加投入し、前工程でのロット滞留を防いでいる。
これは24時間フル稼働体制を前提に生産計画を立てる、我々ならではの苦しい工夫と言える。
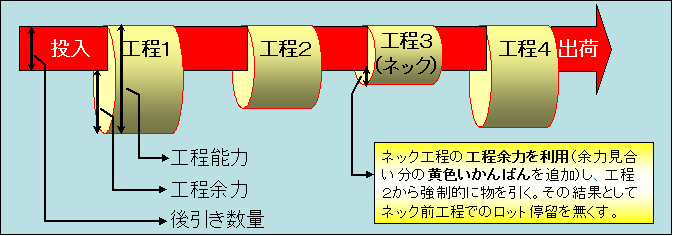
4−2.流し方を変えたら後工程の“引き取りの見える化”も必要に
発想の転換を図ったことにより、前工程は後工程の要求が非常に分りづらくなった。なぜなら、全ての品を欠品としたため、店に混在する後工程の生産指示かんばんから、どの品をどの順番で作業すべきか分らなくなってしまったのである。そこで従来、生産指示かんばん+店の空きを見て作業する品を決めていた前工程は、生産指示かんばん+バーチャルストアと称するモニタを見て作業する品を知る環境に変更しつつある。
5.おわりに
トヨタ生産方式の考え方は普遍だが、私の理解したトヨタ生産方式とは、生産する物や環境、或いはそこで働く人々の違いによって独自の方法論があって然るべき、更に言えば、トヨタ生産方式の実現に向け改革を進める行動そのものであるようにも思う。
岩城先生からトヨタ生産方式のイロハを教わり、どうやって思考を具現化するか一丸となり工夫と努力を重ねて来た。半導体組立で真似できる先進企業に巡り会えなかったことも幸いし、まだ期待する成果には程遠いものの独自のトヨタ生産方式の実現に向け着実に進化していると自負している。現在も “トヨタ生産方式の進化系Nishiki”の確立に向け工場一丸となって取り組んでいる。これは少なからず熊本錦工場のガラパゴス化に拍車を掛けることに違いないが、いずれ「半導体組立の物流し標準」と胸を張って世に問えるレベルに是非とも仕上げたいし、その道筋は見えたと思っている。
1回目の投稿時に岩城先生から頂いた手に余る大きなタイトルが、小心者の小職にとって大きな負担になっていたことは隠しようもないが、1回目の投稿から4年、手に余っていたタイトルに生意気にも自分なりの結論を述べるまでになった意義は大きい。トヨタ生産方式に出会っていなければどんな会社生活を過ごしていただろうか?トヨタ生産方式との出会いに深く感謝しつつ、本4回目を持って一連のシリーズ物としての投稿を終えさせて頂く。
岩城先生コメント
NECセミコンダクターズは、ルネサスと合併等で、その後の活動がどうなったのか心配していましたが、絶えることなく活動が継続しているだけでも賞賛ものであります。
いろいろと試行錯誤しながら、自問自答しているようだが、それを積み重ねるに従い、霧が晴れてくるでしょう。
唯トヨタ生産方式と普通の生産方式の違いは、現場構造上では、横持ちが縦持ちになり、品物流を重要視します。その機能の仕方は、先頭からの押し込みが下からの引きに代わります。この違いによって、トヨタ生産方式では、お客の変動を吸収して、生産を平準化することが出来、ジャストインタイム(各工程の同期)を、自働的(何も管理しなくても)に維持できることになるのです。この原理だけは、いつもしっかり踏まえておきたいものです。
ついでに、平準化するための繰返し頻度が少ないのは、末端ユーザーの使用単位に比較し、半導体工場のロットサイズが大き過ぎることにあります。要は末端のサイズに近づける努力が必要であり、当然現在の半導体工場の構造は、いつかはそれに向かって大改革しなければならなりません。
|
|
「確実に広がるトヨタ生産方式」 |
|
 |
岩城生産システム研究所 岩城 宏一 |
この暮れから新年にかけ、思いがけない人達からの便りを頂いた。それらはいずれも、生産現場の改善状況が書かれていた。それも、改善に対して後退するどころか、益々意気盛んに取り組んでいる内容である。このような傾向は、日本ばかりでなく世界中に、どんどん広がっているのではないだろうか。
先日、静岡でのものつくり懇話会に出席したおり、このような改善の広がりや、活動をしている人々の交流の場が必要であること等が話題になった。この必要性については、もちろん皆が認めることであり、残る問題は具体的に動き出すだけである。
私はこの問題について、今年は一歩踏み出したいと思っている。現在9月に毎年行っているルビコン倶楽部(かってトヨタ生産方式を主導したOBの方の集まり)とトップセミナー(現役の役員クラスの集まり)の開催時期に合わせて、一般の人達の会合を企画したいと思っている
当初は一日で、講演や論文発表程度になるかもしれないが、取りあえず行動に移したいと思っている。参加要領等については早々に成案し、このネット上に公開したいと思っている。その折には、皆さんには積極的に参加して頂きたい。
最後に皆さんからの近況報告で気になることがある。トヨタ生産方式をやっているということは、それはそれで結構なことであるが、大切なことは“会社がはっきり良くなるまで”やってほしいということである。そのためには、正しい改善手法の選択と継続が大切である。
ただ生産現場の無駄をとり生産を向上することだけでは、殆ど経営収支上に効果として表れてこない。目の前の無駄より数段大きな無駄が、生産工場や会社全体には沢山ある。この無駄の削減を優先し、徐々に小さな無駄取りに向かうことである。
経営収支上に効果として効いてこない改善は、改善方法また徹底さを見直す必要があるだろう。要は改善することによって、会社がの決算が良くならないものは、改善したとは言えないと云うことである。
本年もいよいよ本格的に始まった。皆さんの益々の健闘を期待している。
以上
|
|
|
■無断複製・転用・販売を禁止します■
Copyright©Iwaki Production Systems Research Ltd. 2005- |