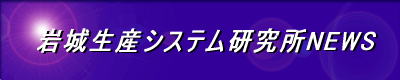 |
発行者 株式会社岩城生産システム研究所
編集者 有限会社IPSインターナショナル |
平成18年2月15日発行 014号 |
|
お知らせ |
岩城生産システム研究所NEWS・第14号を発行させていただきます。
今回は、NEC山口の福原 治美 様及び 弊社 岩城 宏一のコラムを掲載させていただきます。
業務統括部
|
|
|
|
「私、なぜか立っちゃいました」 |
NEC山口
製造部 福原 治美 様 |
 |
Stand play でまた一歩前進
私は半導体製造会社であるNEC山口で、最終検査工程のペレット出荷外観工程を担当しており 顕微鏡による外観検査
作業と製品梱包作業に従事しています。
生産革新の指導会が始まって以来、出荷外観工程と生産革新とは無縁のもので、直接関係することはないだろうとたかを
くくっておりました。ところが、2005年4月の指導会でしょうか岩城先生からいきなり、出荷外観後の店の在庫の量が見たいと
いうことで出荷外観エリアに来られ「そのまま作業を続けて」といきなり作業の指導となったのです。 最初の指導として「振り
返ったり戻ったりと作業のレイアウトがまずい、製品出荷までの作業を直線的な動きにしてください」と言われ、上司の方々が
レイアウト変更を行い、かなり作業性が良くなった事が記憶にあります。
2ヶ月後の指導会の時でございます、椅子に座ったまま横に移動する外観〜梱包作業まで作業を見られ、「もっと楽にして
あげよう!立ち作業にしなさい。その方が体を持ち上げることなく作業ができて楽だから」と指導を受けました。 この出荷外観
工程に5年間従事していますが、今まで立ち作業など考えた事がなく、その提案に驚いて言葉が出ず微笑むのが精一杯で
ございました。
それを察した上司が、作業者の身長格差や体への負担を理由に断ってくれて、私たちの意見を尊重したいと言う上司の言葉に
安堵しておりました。
ところが、そんな上司も12月の指導会で、岩城先生の熱意に根負けしてか「試しに一度、立ち作業にしてみよう。テーブル
を高くするための治具を用意するぞ」と言い出し、驚く反面、その頃には最初ほど立ち作業に対する強い抵抗感がなくなって
おりました。 そしてついに始まった立ち作業、 忘れもしない12月28日に、テーブルの高さが腰の辺りまで高くなりました。
作業に入った当初は足腰の痛みと疲労感から周囲へ愚痴をこぼす事が多くなりました。しかし、年も明け立ち作業を始め1週間
が経過しようとした頃から、腰の痛みも無くなり疲労感にも慣れ、周囲に漏らす愚痴も徐々に少なくなってまいりました。 そんな
ある日のこと、出荷外観作業(外観検査→ウェハーの入替え→梱包の連続作業)を行っていると目の高さが安定している為か、
体の動きが非常にスムーズだと感じはじめました。 流れ棚からの梱包資材をとるため一瞬立ち上がる動作や、製品を顕微鏡
に載せる動作など、立ち上がる事が意外と多かったことに気づきました。
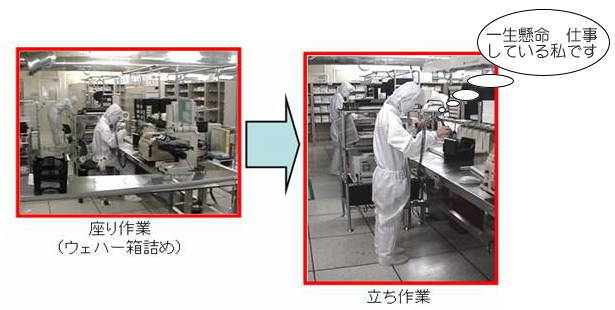
実は、それに気付いた瞬間、電気が走ったような感覚にとらわれました。「岩城先生! これだったんですね」と言いたく
なる思いでした。 「まずは、やってみなさい。」とお叱りを受けたこともありますが 事実やってみると(1)スムーズな動きが
できる。(2)製品と自分の高さが一定の為安定性がよい。(3)慣れからかTOTAL的に楽に感じる。(4)作業スピードUPとたくさん
のメリットを感じております。今では立ち作業がすっかり板についてまいりました。今、まさに「私、なぜか立っちゃいました」
です。
座り作業が当たり前と決め付けていて立ち作業など考えませんでした、余計な先入観は捨てまずはチャレンジすることが
大切ですね。
今回の事で、身を持って体験する事が出来ました。 より良い職場にする為に、生産革新活動に対して今後も一生懸命取り
組み頑張って参ります。 岩城先生 御指導をよろしくお願いします。
以上
|
|
コラム「コンサルタントのひとり言」 |
岩城生産システム研究所
代表取締役 岩城 宏一 |
 |
― 勘違いの無駄・4 (社内請負) ―
|
驚くことに最近では何処の会社に行っても、その会社以外の他の会社から派遣された人達が、大勢働いているのを見かける。
しかも彼らの日々の仕事は、派遣会社の管理者によって管理されており、仕事そのものが請負いになっている場合が多い。
いつも社内に人々を抱えているより、請負は生産量に応じて変動費化できるので、固定費を削減し変動に対応しやすいと考え
た結果でる。しかしこれも大きな勘違いであろう。
このような考え方の背景には、社員であれ請負であれ、人の能力を同一視同していることにある。
このような考え方は、生産現場で働く人々のスキルをまったく無視し、そこで働く作業者を軽視し、スタッフ優先の姿勢
さえ伺える。かつての生産現場では人のスキルの違いを、はっきりと仕事の上で、見ることは出来なかったかも知れない。
しかしトヨタ生産方式に変わった現在では、人々のスキルの重要性は一目瞭然であり、また一定の水準以上のスキルを
保有していない人は、他の人の足手まといにさえなりかねない。
我々がトヨタ生産方式の中で生産革新を行ってきた結果、現在では請負業者の生産能力、生産性、品質等において、
非常に大きな差が生じている。従って請負業者任せでは、とても会社が必要とする生産活動の成果は得られないため、従来
とは違った取り組みがされてきている。
多くの請負の人達は依然としてその工場の中で働いているが、彼らは従来と異なり、その会社の社員と一体になり、高い
生産性や品質目標の実現にチャレンジしている。
今では、生産変動に対し、外部より人を補給することより、現有人員で如何に改善して、それを吸収するかに行動が
変わってきている。
生産変動を変動費で賄おうとする考え方は、生産能力を作業者の人数や設備数をもとに、単純に算術的に処理するもので、
人や設備は活かし方によって限りなく力を発揮するものだと言うことを知らない。
また“変動すること”に対応すること自体、生産活動上最も労力を要することである。
生産量が増加するとき、人の増員や設備の増設に短絡的に走る人は非常に多い。しかし生産変動時、人の増員、設備の
増設自体新たな変動要因を持ち込むことになり、その確保や対応に、非常に大きな労力を費やすことになる。
まず人や設備は変えないで、これらをよりよく生かすことを指向することが、変化への最も楽な対処方法である。
またこのような取り組みは、他を差別化する上で最も重要な活動であろう。
以上
|
|
■無断複製・転用・販売を禁止します■
Copyright©Iwaki Production Systems Research Ltd. 2005- |