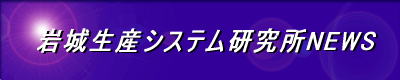 |
発行者 株式会社岩城生産システム研究所
編集者 有限会社IPSインターナショナル |
平成17年12月1日発行 009号 |
|
「どきどき生産に賭ける」 |
株式会社エクセルカイジョー
代表取締役社長 西川 正巳 様 |
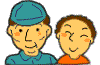 |
当社の生産革新活動である『どきどき生産』とは、あまりお金をかけず、全従業員のチエとアセで、
(1) ムダを徹底的に排除し、
(2) 在庫を極限まで圧縮し、
(3) 場所を最も有効に活用する方法を考え、
(4) 全従業員の力を最大限に発揮することによって、
経営体質の改善を図り、当社の生命を永遠に維持発展してゆくための生き残りをかけた全社的な永続的活動です。
また、在庫を極限まで圧縮していきますので、『同期』を『どきどき』と読むようにし、『ドキドキハラハラ』から改善を楽しむ『ドキドキ
ワクワク』にしていく意味もあります。
『どきどき生産』の目標とする具体的なあるべき姿は、工程の進行に従って、1ヶずつ規則正しく移動するモノの列をより正確に
つくり、その動線をできるだけ短く単純にした『後工程引き取り生産』です。
また、『どきどき生産』では、『従業員が生かされているか』、『従業員が経営に参画しているか』、『情報の共有がなされているか』
を観点とし、集団で発揮すべき共通目標を掲げ、各個人の役割と目標を明確にして、従業員の創造性を発揮できる環境をどうつくる
かを最も大切にしています。
この活動は、1ヶづくりの同期生産を常に追求する姿勢と思い切った行動が必要であるため、当社では、行動指針として『今日は
昨日と何を変えましたか。』を合い言葉に、少しでも変化し続けること。
何を達成したかよりも、何を変えたかを尊重することによって失敗を恐れない行動が根付いてきました。
岩城先生のご指導により、かんばん、流れ棚、レイアウト変更等の具体的な改善要請を一つ一つ素直に実行することにより、
リードタイム、労働生産性、棚卸等の経営数字は、すぐに成果が現れました。
しかし、成果が劇的に変化したのは、自社ルート便の運行、定時定ルートの水すましと内製化の実行を徹底してからでした。
(今は、活動前と比較して生産性20倍以上、棚卸保有日数は1/10以下となっています。)
自社ルート便は、当初10社を廻ってモノを集めていましたが、最初の3ヶ月位はトラックが空っぽの状態で戻ってきました。
当社からモノを引き取りに行っているにもかかわらず、協力会社が当社にモノを納入してくる状況が続きました。
社員からは、経費のムダを指摘されたこともありました。 しかし、粘り強い交渉とルート便の運行を続けるとともに、当社の購買
マンが協力会社に行って、当社で余った机や棚を活用して流れ棚等をつくり、一緒に改善を繰り返すこと50数回を経て、ルート
便での集配が軌道にのってきました。
今では、トラックも最初の軽自動車から普通車になり、信州地区32社を廻るルートが確立され、以前に比べれば在庫(ライン
リーダーは在庫が切れそうで毎日ドキドキすると言っています。)が少なくなってきました。 今年の1月には、雪でルート便が
止まるとラインが止まる。という状況になりました。
現在、取引先をルート便協力会社に集約することによって、さらなる品質向上、コスト削減、在庫削減(保有日数3日)に取り組ん
でいます。
水すましは、定時定ルートで1日14回30分間隔で廻ることにより、仕掛品やモノの停滞が驚くほどなくなってきました。
今は、現場と現場をつなぐだけでなく、情報を伝えるペースメーカーを目指して日々改善しています。
内製化については、私が社長に就任して最初の仕事がトランスの納期督促でした。購買担当のリーダーも納期管理に大部分の
時間をとられ、お客様の要求に対応するのに困っていました。
自分たちでトランスを作ることができれば、納期管理する必要がないという『思いつき』がきっかけで、内製化に取り組みました。
当社にトランス製作の技術はありませんでしたが、完成品を分解して再組立し、評価する試行錯誤を繰り返しました。
試作から2年経過した今では、約70種類のトランスを当社で内製化することが可能になり、製作時間も短縮され、コストダウン
を図ることもできました。(当初2時間かかっていましたが20分で製作できるようになりました。)
また、トランス以外にも、シルク印刷、メッキ、溶接、板金等、かつては外作していたものを自分たちの力で治具、設備を工夫し
内製化しています。
現在はダンボール、塗装など、新しい分野に挑戦しています。考える力は無限であるとつくづく感じました。 このような知恵がでて
きたのも、お金をださないで、社員の創意工夫を信じた結果であると思っています。
今、全社員が一丸となって集中して取り組んでいるのは、次の5つの項目です。
(1) 後工程に不良品を送らないために、問題が発生したときには、『今日のことは今日やり終える』を
合言葉に現地現物での対策による再発防止を図る。
(2) 荷姿改善で開梱作業をなくし、よりスッキリとした現場にする。
(3) 機械加工設備の多数台持ち。
(4) 4つのしかけと4つの約束の徹底。
私を含め管理職以上が毎月1回水すましを実施しながら、改善を進めています。
(5) ライン・流れ棚の間締め。
『どきどき生産』のあるべき姿に対しては、まだまだ20%程度ですが、従業員の知恵と行動のお陰で3年前とは見違える会社に
変化してきました。
この活動を通じて、目の輝いている人が多くなったのが一番の喜びでもあります。
さらなる改革のスピードを上げ、『モノづくりは人づくり』を当社のDNAにし、一日も早く管理しないで管理された状態をつくり、『松本
発世界一』の会社を誰一人の落伍者をだすこともなく全従業員で実現していきます。
以上
|
|
コラム「コンサルタントのひとり言」 |
岩城生産システム研究所
代表取締役 岩城 宏一 |
 |
― 無駄もいろいろ・6 ―
|
さて、さきの号では、通常の生産の中での「今」に対する曖昧さについて説明しましたが、ここでは、トヨタ生産方式における「今」
の定まり方にについて、取り上げてみましょう。
トヨタ生産方式での「今」は、品物の流れをつくり、それによって接続された各工程間で、後工程から前工程に、必要なものを
引き取りに行く動きの中で定まります。
すなわち隣接する二つの工程に着目したとき、後工程が前工程から必要なものを引き取った瞬間から、次に引き取りに来るまで
の時間が「今」の時間の区切りということになります。
したがって、「今」必要なものをつくると言うことは、後工程が引き取りに来るまでの間に、各引き取りの間に、後工程が使う量の
ものを、つくるということになります。
このように、トヨタ生産方式での“今”と言う時間は、通常の場合と異なり、生産が平準化された中で、品物を引き取る時間に
よって刻まれるため、それは非常に正確であり、さらにその時間の長さも、工場内の各工程間では分単位と大変短く、また工場
間でも一日、二日と はっきりした間隔で刻まれている。
この時間が短く、また正確に繰り返されることが大切であり、それは結果的に品物を動かす人や車の、動き方のばらつきを小さく
することになる。このことは、物を動かす人や車の動きが正確度を増し、標準作業として整えられたことになります。
従来の生産における場合と、トヨタ生産方式での生産指示の仕方の違いを、下図に要約しておきましょう。
|
|
「従来の生産方式における場合」
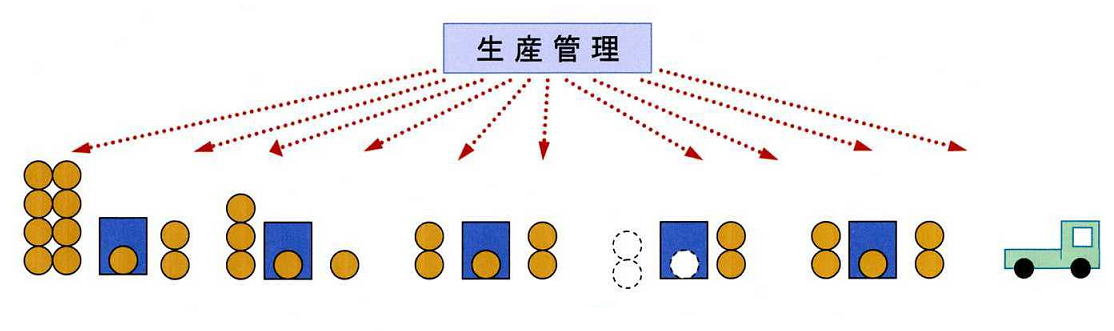
特徴 (1)生産計画に基づき、先頭工程より投入
(2)各工程に仕掛在庫が発生し、これらは出荷の緊急度に応じコントロールされている
(3)全体の出力は、生産管理の采配に左右される
(4)リードタイムは仕掛数が多く、長い
|
「トヨタ生産方式における場合」
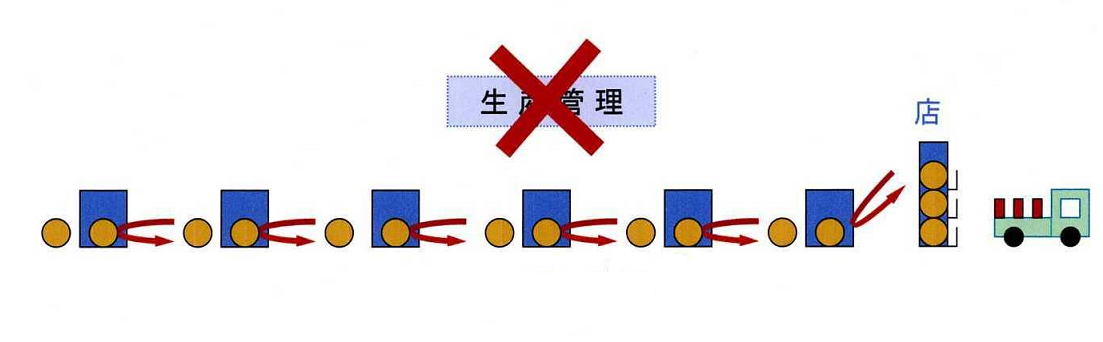
特徴 (1)各工程は加工または組立が終了した状態でワークが保持され、フルワークの状態になっている
(2)最終工程から出荷計画に従いワークが取り出されると、順次
後工程から前工程にワークの引き取りの動きが発生し、
各工程にワークを補充する
(3)全体が後工程の引き取りの連鎖で稼動するため、工場本来の力がそのまま出力になる
(4)リードタイムが1/3程度になる
|
|
このように、通常の生産現場では「今」という時間の定義が曖昧なため、今何をしなければならないことが、はっきりしない
ままに仕事をしているのです。したがって、多くの場合 今の仕事そのものが無駄なことをしており、今はその仕事はしない方が
良いというような大変なことになっているのです。
このような問題の発端は、通常の生産は生産計画で生産し、トヨタ生産方式は“かんばん”で生産していることにあることは、
前に説明した通りであります。
ご存知のように、“かんばん”は部品の取入れから工場の組み立て、さらには顧客まで定期便や“みずすまし”によってつながっ
た品物の流れと一緒に移動し、各工程に直接生産の指示を刻々と伝えています。この点は通常の生産は生産計画とは、大変大きな
違いであります。
しかし、このように“かんばん”が有効に機能するためには、生産の平準化が重要な前提条件であります。即ちこのように効果
的な“かんばん”も、生産の平準化がされないかぎり、まったく使えないということであります。次号では生産の平準化について、
取り上げてみたいと思います。
以上
|
|
■無断複製・転用・販売を禁止します■
Copyright © Iwaki Production Systems Research Ltd. 2005- |